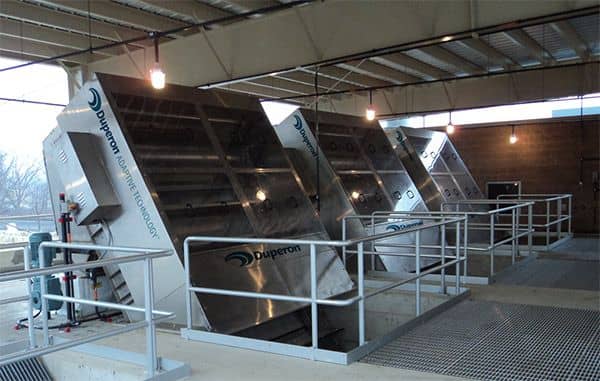
By their very nature, wastewater bar screens are intended to operate under some pretty tough conditions. When a storm surge hits, however, both the severity of conditions and the criticality of results ratchets up several notches. With heavy storms seeming to occur more frequently and with greater intensity, here are multiple points to consider while reviewing mechanical bar screen performance.
No One-Size-Fits-All Solutions
When it comes to evaluating screening solutions for a wastewater treatment plant (WWTP), it is important to note that yesterday’s design solution might no longer meet today’s conditions where peaking factors have impacted WWTPs with up to 20x flows in extreme events.
· Aging Infrastructure. As every wastewater and stormwater collection system ages and wears, the incidence of inflow and infiltration (I&I) tends to increase. Poor connections or settling soil around piping connections can create excessive groundwater infiltration during storm events. Grease and oils flushed down the drain by residents or near restaurant discharges can settle and accumulate with other debris in low spots, only to be flushed out at the beginning of a high-flow storm event.
· Changing Weather Patterns. With four of the top 10 all-time rainfall events in the U.S. occurring since the turn of the 21st century — two of them (tropical storms Harvey and Florence) occurring in the past two years alone — storm surges in wastewater plants should not surprise anyone. Normal seasonal patterns or periodic events, such as El Nino years, can also increase the likelihood of periodic above-average storm runoff . The droughts in the Western US have brought their own share of issues related to wastewater concentration and sub-optimized plant flows.
· Regional Growth. Natural population growth or commercial development that increases the amount of impermeable surface drainage to a combined stormwater/sanitary sewer system can put added pressure on WWTP facilities.
Preparing For The First Flush
Extreme flow events generate a wider range of debris than normal wastewater operations — in terms of individual object size, total volume, and short-term extreme loading (i.e., the “first flush” of debris carried along with the initial wave of stormwater flow). Those factors, plus the fact that the initial surge typically arrives at the screens at a higher-than-normal velocity, can seriously test the reliability of a bar screen system — especially one that is undersized for record-breaking flows that quickly scour debris that has settled in a collection system over time.
Having a well-designed screen solution in place for an anticipated volume of debris is just the first step. WWTPs going from manually cleaned coarse screens to an automated mechanical bar screen with narrow openings will experience a big jump in the volume of debris being collected. Being aware of past experiences and being prepared for a debris-filled initial wall of water on the day of a weather event is just as important for weathering the storm.
· Controls Strategy: In the case of mechanical screens that are designed for wet weather surges, making sure that the screening equipment is in operation before the first flush of water and debris arrives is as important as having the right design in the first place. This can be accomplished through controls logic that can signal to start the equipment before the surge reaches the plant. As an example, using upstream level transducers or tying into the plant SCADA system to indicate when a pump turns on or gate open are sound strategies to start the screen in time to handle the increased flow. Waiting until after the water level at the screen rises could cause the screen to blind over before the machine is turned on. During these peak flow events, it may be advisable to operate at high speed until the conditions stabilize.
· Prepare For The Volume. With the right screen designed to keep pace with the high volume of debris generated by a first flush, ensure that the WWTP is prepared to remove that debris at the rate it is captured. Consider this debris loading while sizing any solids handling equipment, like conveyors, washer compactors, sluices or even dumpsters. This means having enough appropriately sized receptacles to receive that debris as quickly as it comes off the screen.
· Prepare For The Velocity. Testing shows that the ability of a screen to capture debris declines quickly as slot velocity increases. Do not put any upstream restrictions that would create a higher velocity right before the water enters the screen. A restricted opening with head pressure building up behind it can force large debris through at velocities high enough to damage the equipment.
· Prepare For The Composition Of The Debris. Given that the primary objective of a wet-weather screen is to accommodate a surge of the largest and most problematic debris, choose the bar spacing accordingly. If the nature of debris in a WWTP’s storm flow tends to be coarser and denser, like rocks and asphalt, it makes sense to avoid installing a compactor on a dedicated channel.
Design Strategies For Handling The Unexpected
WWTPs looking to install their first mechanical screening system in place of a manually cleaned screen or upgrade an underperforming mechanical screen should take note of the historic impact of storm events on wastewater flows before choosing a new bar screen design.
Because even a few seconds of screening downtime can result in an overflow event, having a mechanical design that can accommodate a variety of object sizes, shapes, and weights is key. That includes large, heavy, and oddly shaped items such as timber, tires, shopping carts, sewer caps, and more. Equipment with mechanical components such as plastic teeth or submerged sprockets is more susceptible to damage/jamming with these types of debris conditions.
Be prepared to address the following factors based on the particular type of debris a sewer system tends to generate during storm events:
· Channel Design Options. If space/design allows, it is not uncommon to have additional channels designed specifically to handle storm flows, separate from the normal wastewater screening flow. That way, the two screens can deliver optimized performance across both normal and extreme flow conditions. Take care that the velocity of wastewater approaching the screen fits within acceptable guidelines for both the channel flow and the slot velocity through the screen. If greater capacity is needed for existing or space-constrained sites, additional volume can be handled by increasing screening area — e.g., widening or deepening the screen field, adding more water depth — or by enlarging the bar openings. Some sites can also evaluate diverting storm flows to some sort of storage basin and recycling it back from that holding area in controlled, manageable volumes once the flow has subsided.
· Bar Spacing. Ideally, bar openings would handle both average and peak flows. Bar screen manufacturers have to size the bar openings to be able to handle peak flow effectively yet also work well in the typical conditions that are seen most days. To handle most flow ranges, bar openings are sized wider for the peak flow although it would benefit the average flows to have smaller openings. So choosing the bar opening is balancing multiple variables (a few primary: plant hydraulics, the ideal slot velocities for a given range, debris characteristics and what solids need to be removed to protect downstream equipment (example, sensitive systems like IFAS system or MBR or something more robust like a pump that can handle 3-inch solids).
· Debris Removal Frequency. Having a wide range of debris removal speed capabilities will help accommodate a screen’s ability to keep up with varying flows and debris conditions experienced among both in dry and wet weather. While the speed of operation is important for removal capacity, so too is scraper spacing. Scrapers spaced closer together effectively clear more debris, as the cleaning frequency is greater. Scrapers spaced wider apart make it easier for the system to capture large, irregularly shaped items.
· Adaptable, Continuous Cleaning. Designs incorporating multiple appropriately spaced scrapers can keep pace with first-flush loads better than single-arm articulating designs that need to travel down and up to complete one cleaning cycle. Keeping both the scraper cleaning pass and the return pass on the front side of the screen will eliminate the possibility of debris falling off the scrapers and into the downstream flow. Look for designs that can handle a wide range of debris encountered in first-flush flows — fully submerged, suspended, and floating.
· Maintenance. With no margin of error for shutdowns during storm surges, choosing a design with low-maintenance requirements and no need for personnel to enter the screen-intake channel can prevent maintenance headaches. For example, avoiding designs with a sprocket at the bottom of the scraper chain eliminates the possibility for timber, rocks, or other hard debris to cause a dead jam condition. Another maintenance consideration is to avoid screens with lots of plastic “sacrificial” components that are susceptible to damage and requires replacement.
· Design Experience. Perhaps the most important design strategy for challenging high-flow events is to team up with an experienced manufacturer who has proven installation experience across a wide range of wet-weather screen applications. The value of that experience will help in evaluating all appropriate options and in calculating the projected performance against the most extreme conditions experienced by the specific WWTP collection system involved.