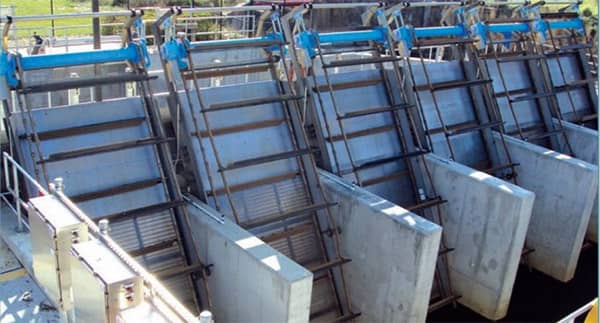
The water industry has made progress in developing numerical values for screen-capture ratings under specific conditions. One such example is the UK Water Industry Research (UK WIR) standard. Its methodology is sound in measuring capture rate for a specific screen in a channel for a specific time and set of conditions.. However, the measurements provided in these studies cannot be assumed to represent the performance of that screen in any other wastewater treatment plant or even in the same channel in a different time or season.
Variables Complicate Standardized Screen Testing
Although the UK WIR methodology is sound, the performance ratings reached there are not necessarily indicative of what actual field performance will be because each plant application is unique with so many variable conditions of debris composition, slot velocities, head loss, and other characteristics. Those conditions vary daily and seasonally, making virtually any rating essentially a snapshot of flow conditions, at a specific time and circumstance.
Daily Variables Based On Flow Rate. The many attributes that impact flow rate and ultimately screen-capture rates and trash-removal rates in practice include:
Time Of Day/Season. Wastewater flows typically follow a diurnal pattern — low in the early morning, rising toward late morning as peak morning use reaches the wastewater treatment plant (WWTP), then dipping slightly in the afternoon before peaking again in the evening. Seasonal conditions affecting flow rates can include precipitation patterns, the increased presence of biological debris such as leaves and grass clippings, and population shifts based on school or resort populations. Figure 1 shows an illustration of a wastewater treatment plants variable flows.
Stormwater. Heavy rainfall events tend to scour the collection system and force heavier debris that has settled in the system to be pushed toward the wastewater treatment plant screens in a concentrated rush. This “first flush” can be laden with everything from gravel to grease bergs.
Effects Of Elevated Flow Rates. Elevated flow rates, whether generated by customer use or sudden rainfall, also impact the dynamics of screen performance and capture rates.
Slot Velocity[SC1] . Particles that are normally captured by a screen when the flow is at the minimum velocity needed to keep those particles suspended can be forced through the same screen at higher flow velocities. This can cause capture rates to decrease as velocities increase.
Head Loss. Beyond the initial velocity of wastewater in the channel approaching the screen, an increase in head loss — the differential between the height of the water in front of the screen and the height of the water behind the screen — will further increase the slot velocity through the screen and in turn decrease the capture rate.
Daily Variables Based On Debris Conditions. Screen capture rates can vary throughout the day based on the volume and the composition of the following debris conditions:
Debris Composition. The composition of wastewater is highly variable by nature — large stones, hair, wipes, plastic trash, timber, stringy vegetation — and each material can behave differently in the flow whether measured alone or in combination with other types debris. Communities have different customs which give a surprising variety plant-to-plant. Industrial processes can also contribute to the debris composition and concentration.
Collection System Attributes. How wastewater gets to the WWTP can have implications on debris conditions and the relative ease or difficulty of screening them out of the wastewater flow. In collection systems that require many lift stations to transport wastewater, debris that has been macerated by multiple pumps can be much finer and more difficult to screen than largely intact debris transported primarily by gravity feed.
Equipment Considerations For Capture and Removal Rates
How screening equipment designers attempt to deal with debris capture influences the performance of that equipment over the long term. Based on the design approach taken, equipment age can also become a factor. For example, machines with brushes and seals can deliver certain removal rates when they are brand new, but that performance level can drop noticeably as parts wear over time.
Front-Clean, Front-Return Equipment. Using a constantly moving device to keep the screening field open, maintains head differential and slot velocities at desirable low levels. Removing and discharging debris on the front side of the screen eliminates the potential for debris carryover. (Carryover is debris that collects on a screen and continues downstream if it is not effectively removed, wreaking havoc on systems and processes that the very screen is supposed to protect.) The capture rate of this style equipment is essentially the same on day 1 as it is on day 1,000.
Front-Clean, Rear-Return Equipment. A front-clean, rear-return screen that operates as a batch system is designed to run intermittently, allowing a mat of debris to build up on the screen in order to capture debris finer than the specified clear opening. Once a level of head loss is achieved, the screen will start moving in slow increments to allow a new mat of debris to build up on the newly exposed screening area.
This type of rear-return design relies on spray nozzles and rotating brushes to remove debris before the screening mechanism returns on the backside of the screen. These screens can be a reasonable and effective solution, but the capture rate cannot automatically be assumed to be the same on day 1,000 as it is on day 1, unless the equipment is properly maintained to ensure optimal operation.
Brushes must be maintained to remain clear of stringy material. This requires operators to check equipment daily and manually remove any materials that catch in the brushes. Operators must also be diligent that brushes remain in full contact with the return screen even as they degrade with age. Brushes that are packed with debris or ineffective can cause carryover and should be replaced.
Spray bars must be adjusted to ensure they clean the screen properly. Operators will need to make sure those spray nozzles remain clean, unclogged, and in proper alignment.
How Screen Design Affects Dynamic Performance
It is impossible to predict the performance of a wastewater screen design without testing every parameter of diurnal flow patterns, slot velocities, head loss, debris characteristics, etc. The physics behind the equipment design will provide clues to how it will react under changing operating conditions.
In a batch operated front-clean, rear-return design, as head loss increases, hydrostatic pressure will start to force debris into the clear openings of a screen instead of simply building up the mat of debris on the face of the screen. Any orifices that remain clear will have water blow through them at higher slot velocities (until they also get intentionally clogged through the matting process). Only when a certain head loss is reached will the screen advance to expose a new clear section of screen. At that point, the newly exposed section will be the path of least resistance for the flow and will experience the highest slot velocities, allowing certain sized debris to be sucked through instead of matting up on the front of the screen.
Debris that is forced into screen openings is difficult to remove. Unless completely removed by brushes or spray nozzles, the debris will be fortified into the openings. Inevitably this debris is carryed over into the clean side of the channel and backwashed by the flow’s hydrostatic forces into downstream processes. The very purpose of any barscreen is to protect all the systems behind it. Carryover by rear-return style screens unnecessarily exposes subsequent equipment to damage and maintenance.
The bottom line is that the screen type and its clear opening size do not change a screening’s inherent capture design. A batch-operated front-clean, rear-return design with any opening size still requires proper maintenance to ensure thorough cleaning or it will retain its inherent risk of carryover. Conversely, a continuously operating front-clean, front-return design that discourages head loss buildup and eliminates the possibility of carryover will behave the same, regardless of its opening size.
Finding The Best Frame Of Reference
Knowing how screen design and wastewater conditions both impact screen performance, how can operators be confident about choosing the best equipment?
The first step it to be cautious about accepting manufacturer performance ratings without knowing the exact parameters of wastewater flow, debris composition, head loss, and slot velocity that went into those ratings. It is too easy to cherry-pick an easy application and favorable conditions that provide a favorable rating on a new piece of equipment.
The best way for WWTP operators to get a feel for real-world capture rates and performance is to request references from WWTP facilities that are already using the type of equipment being evaluated. Questions to ask include:
Has there been a noticeable change in capture rates since the screening equipment was first installed? If so, is it quantifiable, or can the user describe how it occurs?
What type of maintenance is being performed on the screening equipment itself, how much time does it take, and how often is that maintenance required?
What type of maintenance is being performed on clarifiers, digesters, and pumps downstream from the screen, what are the impacts of any debris passing through the screen, and how often is the maintenance required?
What is the total lifecycle cost for the screen design in question and how reliable is it?
Even if a quantifiable capture-rate percentage is available, qualitative information about equipment performance under a range of real-world variables can provide a frame of reference for lifecycle costs of both the screening equipment and the downstream equipment it is designed to protect.