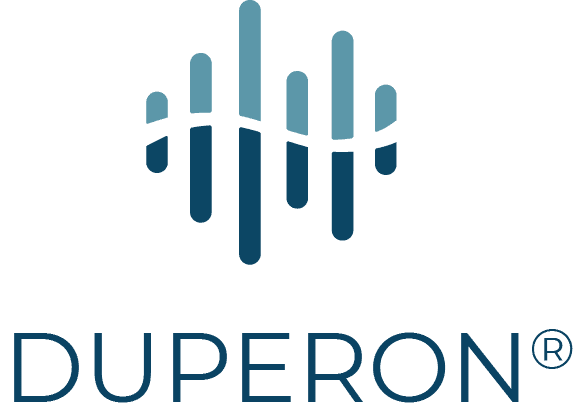
Washer Compactor
Debris Management
The only washer compactor that matches the capacity of the Duperon® FlexRake®
Powerfully simple: providing consistent results in variable flow and debris conditions
Washer compactors help to automate the solids handling process efficiently and provide a bottom-line impact to meet requirements and reduce landfill volume.
The Duperon® Washer Compactor is ideal for debris in wastewater and industrial applications to clean captured screenings, reduce weight, volume, and odors. Since the Duperon® FlexRake® screens can remove large debris, mats, grease, and other irregular items that find their way into the system, our Washer Compactor provides a robust debris management strategy to complete the process.
The patented dual augers provide positive displacement and a self-regulating compaction zone controls pressure, regardless of volume, to deliver consistent results in non-DEO applications. The Duperon Washer Compactor assures captured solids are washed, compacted, transported, bagged or otherwise discharged to your site requirements.
Applications:
- Municipal wastewater
- Combined sewer overflow
- Pump stations
- Lift stations.
- Industrial wastewater
- Other non-standard applications where debris is variable or difficult.
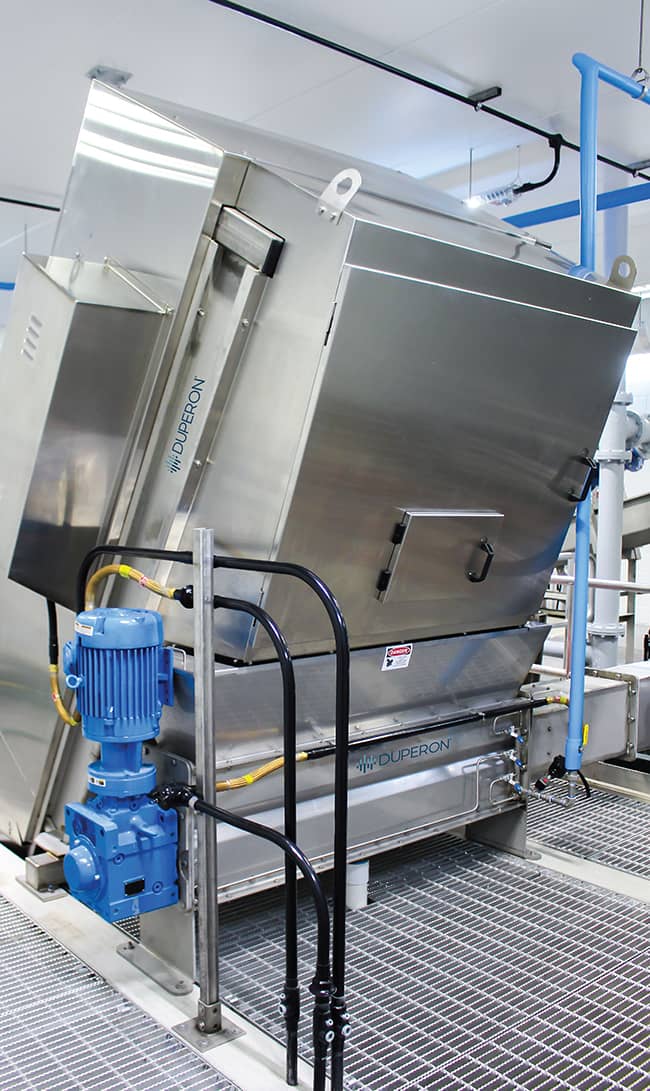
The Duperon®
Difference
The Duperon®
Washer Compactor
Consistent compaction
The self-regulating compaction zone delivers consistent dry solids regardless of debris or volume in non-DEO applications and does not rely on friction from fixed-sized compaction
What goes in, comes out
Positive displacement from patented dual augers processes debris forward, prevents slipping, wrapping, clinging, and bridging
Designed for duty
Designed to process the debris variations that a FlexRake® could occasionally discharge like rocks, grease, clothing, concrete, and metal up to 4 inches
Flexible discharge
The Discharge Extension Option transports compacted screenings up to 40 ft in any direction without additional mechanized conveyance
Low maintenance
A robust dual auger system and bearings assure long product life and minimal maintenance. Strainer is self-cleaning, eliminating brushes
High performance to impact bottom-line
Reliably provides up to 84% volume reduction and 60% dry solids to minimize odor, meet hauler standards, and reduce landfill costs.
Our solutions are simple
Our Solutions Are Simple
The Duperon® Washer Compactor patent-pending Discharge Extension Option (DEO) can transport debris up to 40 feet in any direction, even vertically, eliminating the need for additional motor-driven conveyance systems.
Most washer compactors rely on the debris chute for compaction. This consists of pushing debris through a set orifice to dewater, using friction from the chute to compact, and applying high horsepower motors to move the plug. With this type of equipment, extended discharge chutes would result in over-compaction and jamming.
The Duperon Washer Compactor works differently. The dual augers combined with the geometry of the chute layout produce backpressure. This backpressure allows the weight of the plug column (not friction from the chute) to dewater and compact debris. This allows the DEO to easily transport compacted screenings to extended distances, without resistance, additional conveyance augers/mechanisms or large motors. This makes the DEO an excellent option for retrofit applications with challenging constraints.
The DEO provides significant cost savings by:
- Reducing the length of the bar screen extending multiple levels – the DEO transports the debris to the discharge location instead
- Eliminating additional conveyance, motors and associated Operations & Maintenance (O&M) required
- Eliminates manual labor and debris handling of captured screenings
Duperon continues to lead the industry standard with simple engineered solutions for desired outcomes … all with the reliability that you have come to expect from Duperon.
Description
The Duperon® Washer Compactor is a powerful system that uses self-cleaning dual augers in a counter rotation to prevent wrapping and to help separate organic and inorganic materials. The dual augers use positive displacement, to continuously move debris forward for cleaning, compaction, and discharge. Flood washing ports clean screenings and return organic back to the channel. A proprietary self-regulating compaction zone provides consistent pressure regardless of volume and debris composition in non-DEO applications.
Unlike other technologies, the Duperon Washer Compactor typically compresses debris before it enters the discharge chute so it does not rely on fixed orifice compaction (using the friction of screenings in the chute to compact). The internally controlled compaction allows Duperon equipment to push a plug column with little to no resistance to extended locations. The captured solids are delivered in an enclosed, odor and vector-free chute to the desired discharge point.
General Specs
Typical Applications | Municipal wastewater
Combined sewer overflow Pump stations Lift stations. Industrial wastewater *Other non-standard applications where debris is variable or difficult. |
Sizing | 3 body sizes to choose from to accommodate site and flow capacities. |
Water | Utilizes filtered effluent or municipal water
Washer consumes 3-10 gallons per minute Requires 40 PSI-60 PSI Drain connection 3” NPT Supply connection 1/2” NPT |
Utility | 120/240 volt, single phase
240/480 volt, three phase (0.6 kW/2.3 kW/3.8kW) |
Drive | 1 hp, 3 hp, 5 hp inverter duty motors available |
Material of Construction | 304 SSTL or 316 SSTL
SSTL spur gears (17 – 4 PH) Self-lubricating main auger bearings |
Bar Screen Flows | Flows up to 100 MGD*
*flow values are based on MOP8 values through a ¼” bar screen |
Peak Capacity | Available from: 30 ft3/hour to 150 ft3/hour |
Typical Performance | Up to:
30% – 60% dry solids 60% – 70% weight reduction Significantly decreases odor and fecal content |
Standard Controls | Packages range from simple start/stop to sophisticated automation.
Motor overload protection provided. |
Operation Options | Continuous while screen is running with off-delay capability to clear hopper |
Key Features
Designed to handle the debris variations that a FlexRake® could potentially discharge
Positive displacement from counter-rotating dual augers ensures what goes in, comes out
Dual augers stress and stretch debris without chopping or grinding
Self-cleaning strainer uses direct contact with the lower auger to keep clean, eliminating maintenance intensive-brushes and relieve strainer clogging.
Housing geometry reduces potential for “Slip Flow” when processing grease, septage and other similar debris
Continuous operation, non-batching system – no buildup of debris, no overflowing or odor issues
Operates in sync with FlexRake bar screen
Passes paint filter test
Accessories
This option is available for the Duperon® Washer Compactor and can transport debris up to 40 feet in any direction, even vertically, eliminating the need for additional motorized conveyance systems.
The Bagger System attaches to the discharge chute for applications where bag dispensing and odor control are required. Included is a 90 meter length of continuous feed bags.
This flexible Drop Sleeve is an economical way to direct and contain downward debris discharge. Also used where waste container hauling may cause damage to metal discharge chutes.
The washer compactor housing and chute can be thermally protected from cold temperatures with the addition of the Heat Blanket with integral heat trace.
Other options include: Operating hopper bypass and hopper level sensor
Schematic
Photo Gallery
Case Studies
Bay County Department of Water & Sewer Case Study
The Washer Compactor Discharge Extension Option easily transports compacted screenings 35 ft vertically without additional mechanized conveyance. The screenings delivered to grade are cleaner, drier, and lighter weight.
Related Products
RFQ form
You’ll like
working with us
Before we installed the Duperon® Washer Compactor, we’d fill a dumpster with wet garbage and rags. It just makes a nice, dry discharge… We’re quite pleased with the application
Doug Koss
Operations Supervisor, Bay County Department of Water and Sewer
Tell us about your project
‘You’ll like working with us’ is a commitment and the way we deliver extraordinary customer care for the full life-cycle of your equipment. This is how we strive to earn the privilege to serve your continued screening needs.
Design Collaboration
To build your solution, our engineers take the time to understand your facility, process, and goals.
We’ll combine our team’s experience with water screening, cleaning, and processing with your team’s detailed understanding of your product and process, so we can develop a reliable and cost-effective solution.